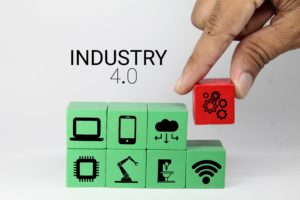
In a constantly changing world, industries are the first to benefit from this development and sometimes bear the consequences.
Today, many industries are suffering from obsolescence of their equipment. A problem that weighs heavily on operational production processes, as well as on the budget management of companies.
Obsolescence is no longer limited to electronic components, but also affects a growing number of various equipments, such as electricity, electromechanics, lifting hardware and tapes. A reality that thus complicates the maintenance of equipments, intended for operation beyond the life of the parts that constitute them.
The management of equipments’ obsolescence is an important setting for the profitability of industrial companies, thus making it possible to reduce the various risks that this can entail, to avoid any malfunction and to anticipate any operational shutdowns.
To respond to this problem, EcoSpare offers you the answer via a multidimensional analysis that begins with an identification of the risks generated by the obsolescence of industrial parts while providing an effective and efficient management plan.
These days, it is getting harder to survive in markets flooded by competition and ever-changing industrial ecosystems.
An evolution favorable at first glance, but rather overwhelming in the framework!
Innovation and mastery of new technologies immediately became the new commercial weapon of equipment suppliers. Thus, the latter offer their customers products aligned with new trends and even more efficient and effective in terms of functionality, speed and energy consumption. However, one should never put into oblivion the hidden facet of any commercial discourse that one tries to cover up. Each new generation of product has a shorter life cycle than the previous ones, making them obsolete. On the one hand, suppliers must constantly offer their clients new generation products in order to maintain an advantage over their competitors and on the other hand, keep a large stock of spare parts for their old series.
A dilemma permeated by financial, logistical and evolutionary factors.
For industrial companies, the ambition is to make the best investment. The main objective when acquiring new equipment comes down to its operational lifespan. The latter must be as long as possible while maintaining the same level of quality and safety. An optimistic vision, but far from agreeing with the approach of their suppliers.
Today, it is the manufacturers who suffer the most from the costly consequences of this scourge, which strongly impacts their portfolios and their operational processes.
Therefore, it is elementary to take this situation into consideration before investing in any equipment.
Developed by us, EcoSpare offers you an obsolescence management plan for industrial parts that will allow you to detect the risks of obsolescence as early as possible and to fix them.
To cope with the significant increase in equipment obsolescence cases, we suggest that you set up a proactive obsolescence management plan that will provide you with a solution to your problem while saving costs and protecting the environment:
“Prevention is better than cure” This is the adage to adopt when dealing with the obsolescence of your equipment. Before investing in any equipment, a purchasing strategy is essential, allowing manufacturers to protect themselves from the risks generated by this scourge.
When purchasing, it is better to be well informed about the lifespan of the equipment you are going to acquire. We have seen manufacturers who bought equipment launched on the market a long time ago and who have only one year left before the end-of-sale announcement. These same manufacturers found themselves with equipment that had to be changed 2 years after being put into service!
Preventive maintenance is essential before your equipments exceed their useful life. The obsolescence and failure reflected in the increasing rate of malfunction and the increasing maintenance costs. It should not be overlooked that the failure of a single part can shut down the activity of an entire factory and automatically its production.
Therefore, it is necessary to conduct a global audit to know the current state of its systems, to identify the machines that are already obsolete, to know how long its components are already on the market, to prioritize according to failure risk rate and its causes in order to offer suitable solutions in terms of quality, costs and time. Questions that technicians must constantly ask themselves in order to perform analyzes and tests, allowing them to identify the condition of the equipment and define the intervention period.
To optimize results, preventive maintenance must be overseen by technicians who have the expertise necessary for the management of the equipment, the managers as well in the different phases of their life cycles. It is often observed that companies do not have internal experts who can devote their know-how to training new technicians. In this case, it makes sense to call on external resources to conduct this mission.
Often underestimated, a trained workforce is able to improve performance and optimize key indicators (downtime, on-time deliveries, rejection rate, etc.)
Setting up a stock and supplying it regularly can be costly, but it remains with no doubt the most effective preventive means in the case of obsolescence of a key part.
Note that an inefficient parts management process can increase downtime by 15-35%.
To compensate for any operational stoppages, maintaining a stock of spare parts remains an optimal solution to intervene at the right time.
In the long term, take advantage of any replacement of obsolete components to supply a provisional stock of repair parts.
Either way, obsolescence is almost inevitable. Industrial parts that are no longer in a condition to be used by clients and that the supplier cannot support, will eventually no longer be supplied and will find themselves victims of wear or a new sanitary standard.
When equipment becomes obsolete, two solutions are probable:
You can always attempt a replacement by going to specialist parts companies that have huge stocks, even long after official support has been turned off.
Spare-Place is the best answer to this need. Spare-place is the first French Marketplace specialized in the sale of new, obsolete or used industrial parts, containing more than 10,000 references.
If no replacement is possible and you decide to renovate your systems, just contact EcoSpare that will take charge of the recovery of your dead stock, its refurbishing and its upgrading. As a result, you will get rid of your unused stock while participating in the circular economy and improving your CSR record.
Managing spare parts obsolescence is a puzzle for any business, regardless of its field. They must have the ability to resolve their technical problems as quickly as possible for the best price, in order to maintain client satisfaction.
Need help making it? Visit spare-place.com!
Monthly Newsletter